Table of Contents
Die cutting is a versatile manufacturing and crafting process that has revolutionized the way shapes and designs are created across a variety of industries. From packaging and printing to intricate crafts and industrial applications, die cutting offers precision, efficiency, and customization that traditional cutting methods simply cannot match. In this article, we’ll break down what die cutting is, how it works, and why it remains a critical process in modern production.
What Is Die Cutting?
Die cutting is a process where a specially shaped blade, known as a die, is used to cut material into specific shapes. This method allows manufacturers and designers to produce consistent, high-quality shapes quickly and cost-effectively. Originally developed for the printing and packaging industries, die cutting has evolved to accommodate a wide range of materials—from paper and cardboard to fabric, foam, and even metal.
Key Points:
- Definition: Die cutting uses a custom-made die to cut out shapes from a variety of materials.
- History: The technique originated in the printing and packaging sector and has expanded into many creative and industrial fields.
- Terminology: Common terms include “die,” “press,” “matrix,” and “cutting edge,” all of which are integral to understanding the process.
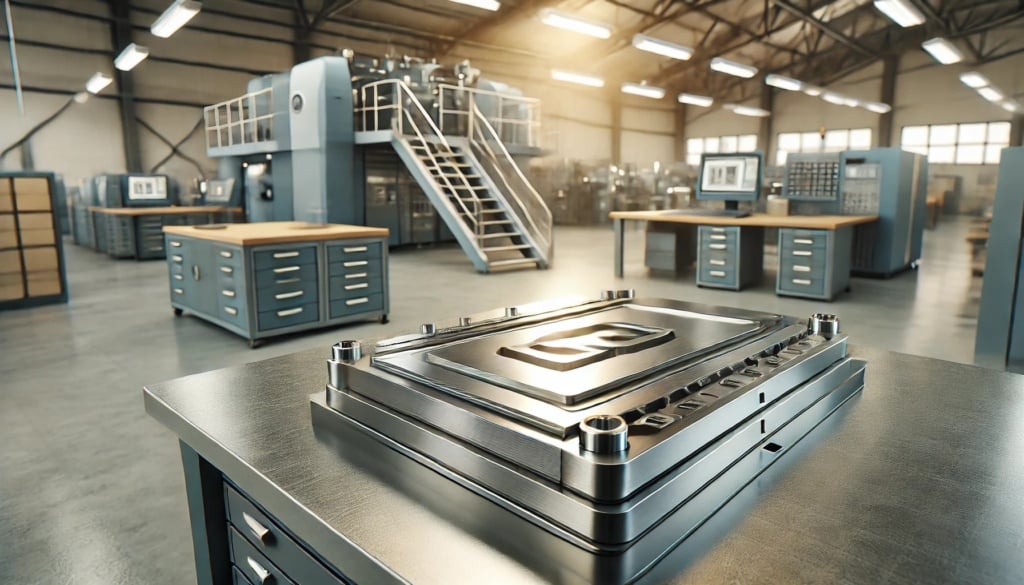
How Does Die Cutting Work?
At its core, the die cutting process involves creating a die that embodies the desired shape. This die is then pressed onto the material, cutting through it with remarkable precision.
The Process:
- Design & Die Creation:
A design is first conceptualized and then transformed into a die. Dies can be made from various materials, with steel rule dies being among the most common. - Material Placement:
The material (whether it’s paper, fabric, or another substrate) is laid on a flat surface or fed into a die cutting machine. - Cutting Operation:
A press or machine forces the die into the material. The pressure cuts through the material along the die’s outline, creating the finished shape. In automated systems, computerized controls ensure the cut is consistent every time. - Quality Control:
Post-cutting, the products are inspected for consistency and quality, ensuring each piece meets the required specifications.
Visual Aids:
Incorporating diagrams or step-by-step illustrations can help readers visualize the process and understand the mechanical precision behind die cutting.
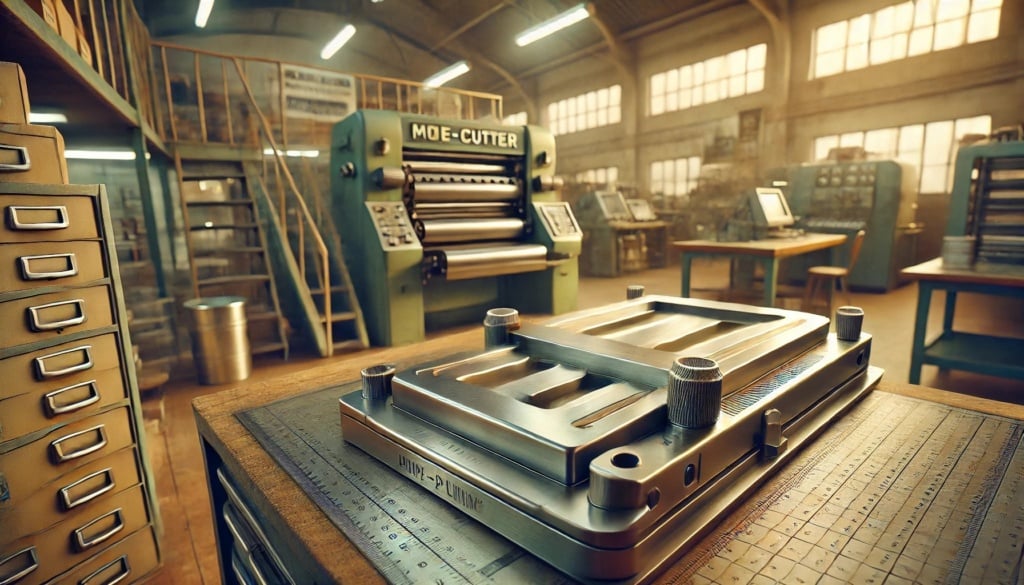
Types and Techniques of Die Cutting
Die cutting is not a one-size-fits-all solution. Various techniques and technologies have emerged to address different needs and applications.
Manual vs. Automated Die Cutting:
- Manual Die Cutting:
Traditional hand-operated methods that are often used in small-scale or craft applications. - Automated Die Cutting:
Modern, computerized systems that handle high-volume production while ensuring accuracy and speed.
Different Cutting Techniques:
- Rotary Die Cutting:
Utilizes a cylindrical die that rotates to cut materials, ideal for continuous cutting. - Flatbed Die Cutting:
Uses a flat die and is suited for thicker or more delicate materials. - Laser Die Cutting:
Employs lasers to cut complex shapes with high precision and is particularly useful for intricate designs.
Materials and Dies:
- Materials:
Die cutting can be applied to paper, cardboard, fabric, foam, and even metal. - Dies:
Available in various forms—such as steel rule dies or laser-cut dies—each suited for different applications and production volumes.
Key Benefits and Advantages of Die Cutting
Die cutting offers numerous benefits that have made it indispensable in various industries.
Efficiency & Precision:
- Speed:
The process is fast, allowing for high production volumes. - Consistency:
Each cut is uniform, reducing errors and waste.
Cost-Effectiveness:
- Reduced Waste:
Precise cuts mean less material is wasted during production. - Lower Labor Costs:
Automated systems can perform tasks faster and with fewer errors, reducing labor expenses.
Customization & Versatility:
- Unique Designs:
Custom dies can produce intricate shapes tailored to a company’s branding or project needs. - Wide Applications:
Whether it’s packaging, signage, or crafting, die cutting adapts to a multitude of requirements.
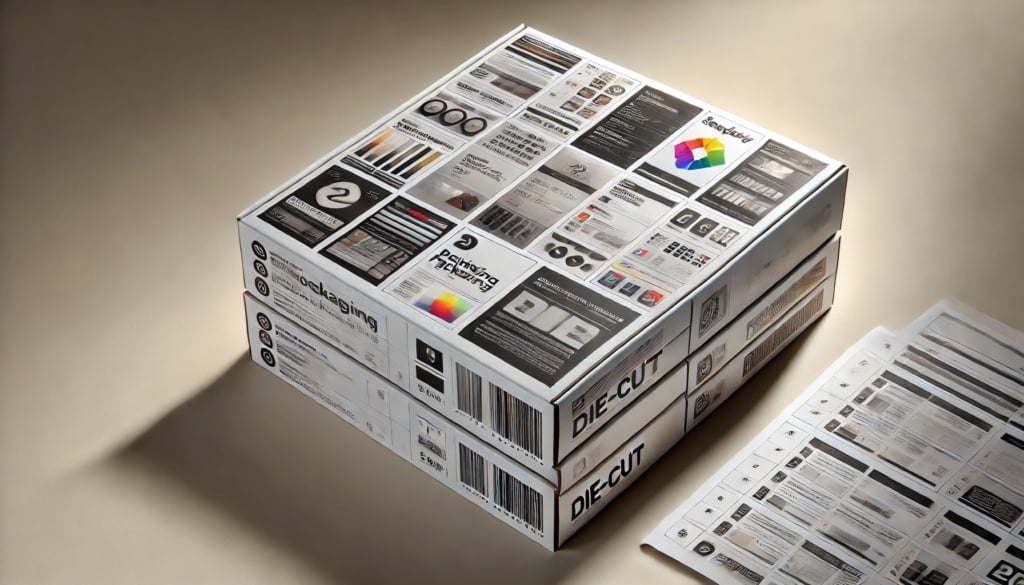
Applications and Industries That Use Die Cutting
The range of industries that benefit from die cutting is vast and varied.
Packaging & Labeling:
Die cutting is essential in the creation of custom packaging, labels, and inserts. It helps brands stand out on shelves with uniquely shaped packages that are both functional and aesthetically pleasing.
Printing & Stationery:
From business cards and invitations to brochures and posters, die cutting is used to add an extra dimension of creativity and professionalism to printed materials.
Crafts & Manufacturing:
For hobbyists and manufacturers alike, die cutting opens up possibilities in custom signage, scrapbooking, fabric design, and more. Its versatility is particularly valued in industries where intricate and repeatable designs are key.
Die Cutting vs. Other Cutting Methods
Understanding the differences between die cutting and other cutting methods is crucial when deciding on the best process for your project.
Comparison with Digital Cutting:
- Traditional Die Cutting:
Offers physical dies that provide tactile precision and is often preferred for high-volume production. - Digital or Laser Cutting:
Uses computer-controlled lasers to cut materials without the need for physical dies, offering greater flexibility for short runs or complex designs.
Suitability for Various Applications:
Die cutting tends to be more cost-effective and reliable for large-scale projects, while digital cutting might be ideal for custom, one-off designs.
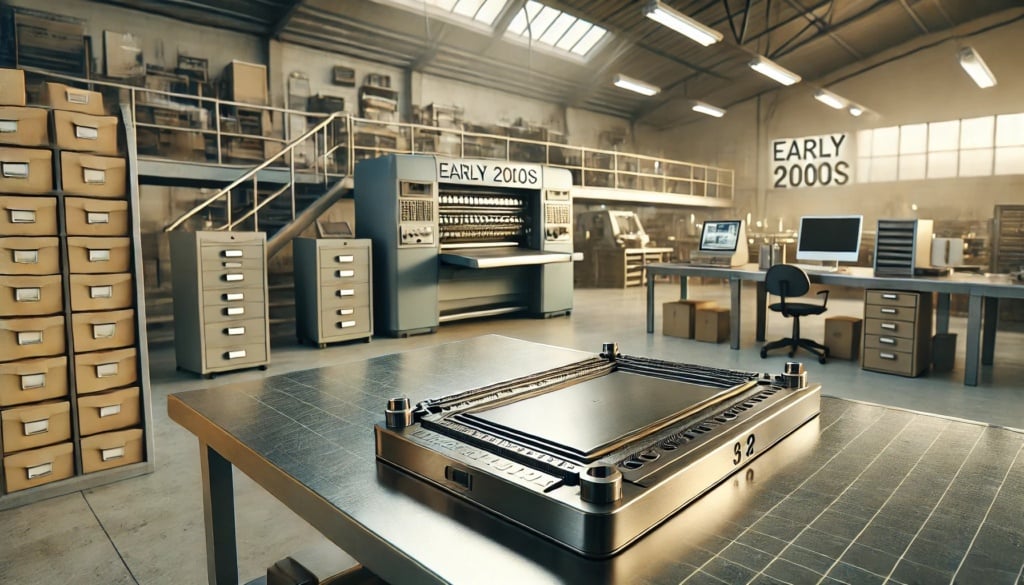
Best Practices, Common Challenges, and Future Trends
To get the most out of die cutting, it’s important to follow best practices and stay aware of the challenges and emerging trends in the industry.
Best Practices:
- Selecting the Right Die:
Choose a die that matches your material and design requirements. - Maintenance:
Regularly inspect and maintain your equipment to ensure longevity and consistent performance. - Process Optimization:
Continually assess your cutting process to identify and eliminate inefficiencies.
Common Challenges:
- Die Wear and Tear:
Over time, dies can become dull or damaged, impacting cut quality. - Material Inconsistencies:
Variations in material thickness or composition can lead to irregular cuts. - Troubleshooting:
Addressing issues promptly is key to maintaining production schedules and quality standards.
Future Trends:
- Increased Automation:
Advances in robotics and AI are likely to further enhance precision and speed. - Sustainability:
Eco-friendly materials and processes are gaining traction, pushing the industry toward more sustainable practices. - Integration with Digital Design Tools:
Seamless integration between design software and die cutting machinery is set to streamline production and boost creativity.
Conclusions
Die cutting is more than just a manufacturing process—it’s a powerful tool for innovation and creativity. By offering speed, precision, and the ability to produce unique designs, die cutting continues to be a cornerstone technology in industries ranging from packaging to personalized crafts.
Key Takeaways:
- Understanding the Process:
Die cutting’s efficiency and consistency make it an ideal choice for large-scale and detailed projects. - Versatile Applications:
Its adaptability across various materials and industries underscores its widespread utility. - Embracing Innovation:
Staying current with technological advancements ensures that businesses can maximize the benefits of die cutting.